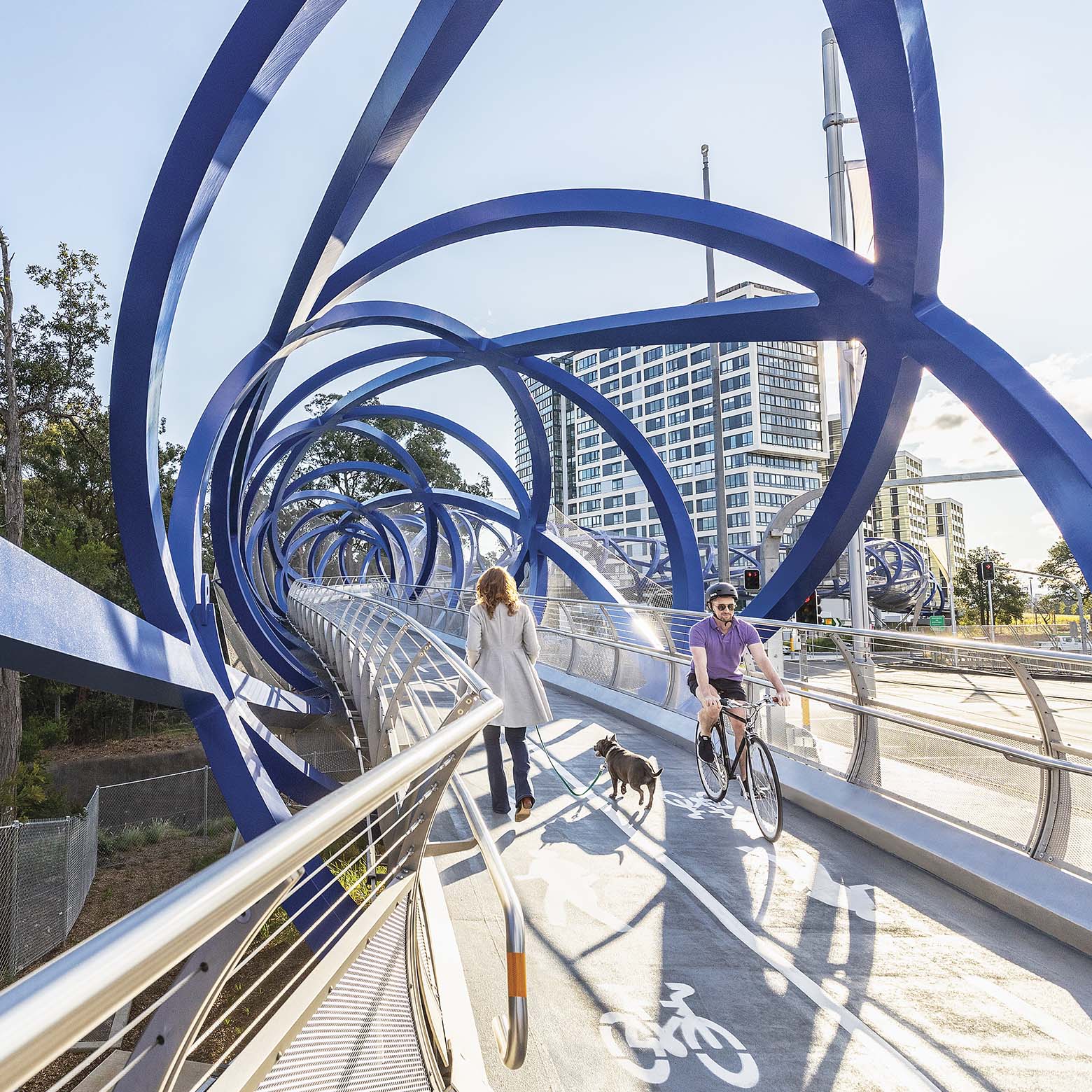
Deakin University Pedestrian Bridge
The use of BlueScope REDCOR® weathering steel to construct a pedestrian bridge at Deakin University’s Burwood campus has helped overcome a contentious and protracted community debate, to provide an accessible crossing over Gardiners Creek.
Words: Rachael Bernstone.
Photography: Lisbeth Grosmann; Peter Hyatt
Project Summary
watsonarchitecture+design’s inclusion of BlueScope REDCOR® weathering steel to enhance pedestrian access to Deakin University has resulted in a bridge boasting rich, red tones and the unusual ability to both blend in and stand out.
Above and Beyond
Morgan’s Walk - the new pedestrian bridge that links Deakin University’s Burwood Highway and Elgar Road sites, divided by Gardiners Creek - is a triumph in one more ways than one. The elegant and efficient design - which uses REDCOR® weathering steel to great effect - helped to overcome several major challenges including access for construction, the issue of ongoing maintenance and, perhaps most importantly, public opinion.
The long and drawn-out story began in 2004, when the University announced plans to build a replacement bridge across the creek corridor. At that time, there was a small bridge at creek-level accessed via walking paths on either side. More than 40,000 people - staff, students and locals - used the crossing each day, but as it was accessed by steps on the Elgar Road bank, it was inaccessible to people using wheelchairs and prams, or those with other mobility issues.

A competition was held and a winning scheme selected, however that proposed design failed to achieve planning approval from Whitehorse Council because of community concerns about the weight and visual imposition of the design for the bridge, which meandered across the gully in line with the treetops. In 2012, the University approached Melbourne architect Rob Watson, director of watsonarchitecture+design, to discuss plans for a lighter, less visually imposing structure, and those plans progressed to become the bridge that graces the crossing today.
Construction began in late 2016 and the new bridge - called Morgan’s Walk in honour of former Deakin University Chancellor David Morgan AO - officially opened in 2017.
For architect Rob Watson, this was a dream commission. As a young architect working in the London offices of Grimshaw and Foster + Partners, he worked on projects such as the British Pavilion for the 1992 World Expo in Seville and Germany’s Reichstag Refurbishment, during which time he was exposed to projects where structural expression and exacting attention to detail were paramount. These characteristics are still of the utmost priority in all of his projects and this bridge represented an ideal opportunity for them to be distilled and even further refined.
This project represented a particularly difficult design problem, Watson says, because the new bridge had to address three major obstacles. The first was access: it had to comply with the requirements of the Disability Discrimination Act to provide safe and easy passage for people of all abilities. Secondly, because the creek corridor is titled Crown Land (the University owns the parcels on either side) the flyover section had to be low maintenance and easily accessible, to avoid protracted and costly access permits. Thirdly, the bridge had to blend in with its native bush surroundings, an especially important consideration to ensure community support for this design.
As part of his solution to address these challenges, Watson chose to build the new 250-metre long bridge using weathering steel, including approximately 200 tonnes of REDCOR® weathering steel in grade WR350L0 and HW350. Weathering steel, when used in the correct environment, requires little maintenance over its lifespan compared with traditional structural steel, and its appearance helps the bridge blend into the native bush surroundings.
Weathering steel requires little maintenance over its lifespan and its appearance helps the bridge blend into the native bush surroundings.
Watson devised an innovative 3D structural system that includes a 200-metre long bridge section spanning over the 85-metre wide parcel of Crown Land - touching the ground at just one point via two V-shaped steel pylons - that minimised the bridge’s impact on the creek corridor, both during initial construction and throughout its projected lifespan.
“While there are some excellent paint systems available for steel structures, on this project any painting would have been problematic,” Watson says. “The bridge has a lifespan of 100-plus years, so it would have needed to be painted perhaps three or four times during its life. Not only did the REDCOR® weathering steel provide an acceptable appearance to the community, that it requires virtually no maintenance was very appealing from a design and whole-life perspective.”
The bridge comprises a series of repetitive modular bays – each about four metres-wide by six metres-long - that were connected to form a series of six trusses, ranging in length from 16.5 metres to 47 metres. Each modular bay consists of two concrete decking panels cast into six folded trays of permanent formwork made from REDCOR® weathering steel in grade HW350. These permanent formwork trays give the underside of the bridge the same appearance as the rest of the structure, so that the weathering steel finish is visible from every angle.

Like the entire bridge, the junctions were designed to appear elegant and efficient, particularly because access for future maintenance would be limited, Watson explains. “There was a lot of discussion about the detailing,” says Watson. “Even though it’s a simple structure - in the way it’s modulated as a 3D truss - we wanted to inject some form into it for practical reasons. I’m a big admirer of engineering design where structures have beauty, because with a bit of thought you can make these things look elegant. At Grimshaw’s and Foster’s offices, we used to slave over the details and we took that approach here.
“We studied every junction carefully, to make them look as elegant as possible and so as not to trap water or dirt,” he says. “Originally, Macalloy bars were designed to tie V-pylons together, but in conjunction with Kane we decided to go with 32mm-thick plates of WR350L0 grade REDCOR® weathering steel with a pin joint, using 85mm diameter Duplex steel pins to tie the heads of the two V-pylons.”
Rob Watson’s vision was turned into a buildable reality with structural engineers WSP Structures; modelled and steel-detailed by PlanIT Design Group; fabricated off-site by Sutcliffe Engineering; and erected by Head Contractor Kane Constructions, with Associated Rigging and Metcalf Cranes.
According to Kane project manager, Mark Spolidoro, the unusual and complex geometry of the bridge posed different challenges to Kane’s regular projects, which include significant health and education facilities. That complexity was compounded by the fact that access to the creek-side walking paths and the existing crossing had to be maintained throughout construction. “I wouldn’t say it was easy, but we planned it all in minute detail and each plan was meticulously peer-reviewed by independent members of our team. We didn’t have any major issues on-site,” Spolidoro says. “But I had a few sleepless nights before we started.”
“I’m a big admirer of engineering design where structures have beauty, because with a bit of thought you can make these things look elegant.”
Rob Watson watsonarchitecture+design
As the project moved towards the site erection stage, Kane, along with Associated Rigging and temporary works engineer Andrew Baigent, devised a detailed works sequence and methodology plan that outlined each step in the rigging process, focusing on safety and build-ability. “The tolerances we were working with were minimal,” Spolidoro says. “From pin to pin, between the tie member plates - a distance of approximately 28 metres - we had a tolerance of just 1mm.”
The bridge supports and walkway truss bays were transported in lengths of about 25 metres and a decision to change from welded truss splice connections to bolted connections shaved two weeks’ worth of site welding from the program. After the trusses were bolted together on the ground, the sections were lifted into place by one of Australia’s largest mobile cranes - Metcalf Cranes’ 600 tonne Demag TC2800-1 - which was located in a carpark on the Elgar Road side for just over two weeks.
“That was a very intense period,” Watson recalls. “We had a huge mobile crane on the embankment, not because of the weight of the parts, but to reach 65m into the creek corridor, sometimes with 50 metre-long elements hanging off the jib.

“Once the V-pylons and four middle truss sections were in place, Kane shifted to 350 and 200-tonne cranes for the remaining sections,” Watson explains. “The deck trays went on progressively after each truss section was installed, providing a safe working deck. The deck trays are made from 3mm-thick REDCOR® weathering steel in grade HW350, which was fabricated into form like 140mm-deep baking trays, to act as permanent formwork for the concrete deck panels.”
As a result of Watson’s fully integrated and symmetrical structure, the bridge appears to extend effortlessly across the creek corridor. From a distance, and from certain vantage points along the creek-side walking paths, it can be seen protruding delicately above the tree canopy. The hovering effect is amplified by the integrated hand-rail and safety enclosure system, which features ‘barely there’ frameless 17mm-thick clear glass panels mounted on hinges at the base so the glass can pivot inwards for cleaning. “From a distance, all you can see is the structure and the people walking across it,” he says. “It looks deceptively simple, but it took a bit of work.”
So after a false start and initial community backlash, Deakin University’s Burwood campus and local residents finally have a bridge across Gardiners Creek that is accessible to everyone. And, according to local news reports, the community is pleased with its striking weathering steel structure that boasts the unusual ability to both blend in and stand out.
The bridge was officially opened by planning minister Richard Wynne and the University’s vice-chancellor, Professor Jane den Hollander AO, in August 2017. Minister Wynne explained that the government had intervened at the planning stage because the project was too important to the University and surrounding community to be held up by bureaucracy. “This is a great advancement for one of Melbourne’s flagship universities,” he says. “For too long, people living with a disability, the elderly or people with prams have been without a suitable crossing over the Gardiner’s Creek Reserve.”
Professor den Hollander says that the bridge has strengthened ties between the university and local residents by removing the bottlenecks caused by peak traffic over the creek from the local walking paths that run alongside it. “With the development of the pedestrian crossing, the traffic jams of students – upwards of 40,000 pedestrians a week in peak time – will be taken off the ground and out of the way of community members walking dogs, exercising and enjoying their beautiful reserve.”
Panel Says
The contribution of REDCOR® weathering steel to create this delicate pedestrian bridge demonstrates an ideal use of this material, which is sometimes specified for its aesthetic properties and rich, red tones. REDCOR® weathering steel is particularly successful in this application because the weathered finish sits confidently and comfortably within the bushland setting, almost hovering amongst the treetops, and the steel will require low ongoing maintenance over its lifetime.
Thanks to its graceful modular form, this new bridge provides a solution to an everyday problem: how to transport pedestrians across the creek in a low impact, uplifting and expressive way.

Project information
Architect
watsonarchitecture+design
Project
Deakin University Pedestrian Bridge, Victoria
Location
Deakin University, 221 Burwood Hwy, Burwood VIC 3125 View on Google Maps
Copyright © 2018 BlueScope Steel Limited ABN 16 000 011 058. All rights reserved.
No part of this publication may be copied, reproduced or distributed without consent. BlueScope Steel Limited, to the extent permissible at law, is not liable to any person for loss or damage arising from reliance upon information contained in this publication. The articles featured in this edition of STEEL PROFILE® are sourced, written, fact-checked and curated by the authors with editorial contribution from BlueScope Steel Limited. Any statements or opinions attributed to a person are the views of that person alone and do not necessarily reflect those of BlueScope Steel. The decision to use any particular product or material in the projects featured in this publication was made by the team involved in each project and not BlueScope Steel Limited. While care has been taken to verify the accuracy of details in this publication, BlueScope Steel Limited assumes no responsibility or liability for any errors or omissions in the content of this publication. All information is provided with no guarantee of completeness or accuracy.
Images shown throughout have been reproduced to represent actual product colours as accurately as possible. However, we recommend checking your chosen colour against an actual sample of the product before purchasing, as varying screens and devices may affect colour tones and finishes.
Every project is different and not all products are suitable for all applications, projects and environments. You should confirm the suitability of particular products for your project by contacting the supplier directly and by obtaining information and advice specific to your circumstances.
To determine whether a BlueScope warranty may be available for use of a product in your particular project, please visit bluescopesteel.com.au/warranties.
BlueScope and REDCOR® are registered trademarks of BlueScope Steel Limited.
Submit your project
We encourage you to share your projects for consideration in a future issue of STEEL PROFILE® magazine. We invite you to submit projects that feature a ground-breaking or an innovative use of steel. We love celebrating and writing about such projects!